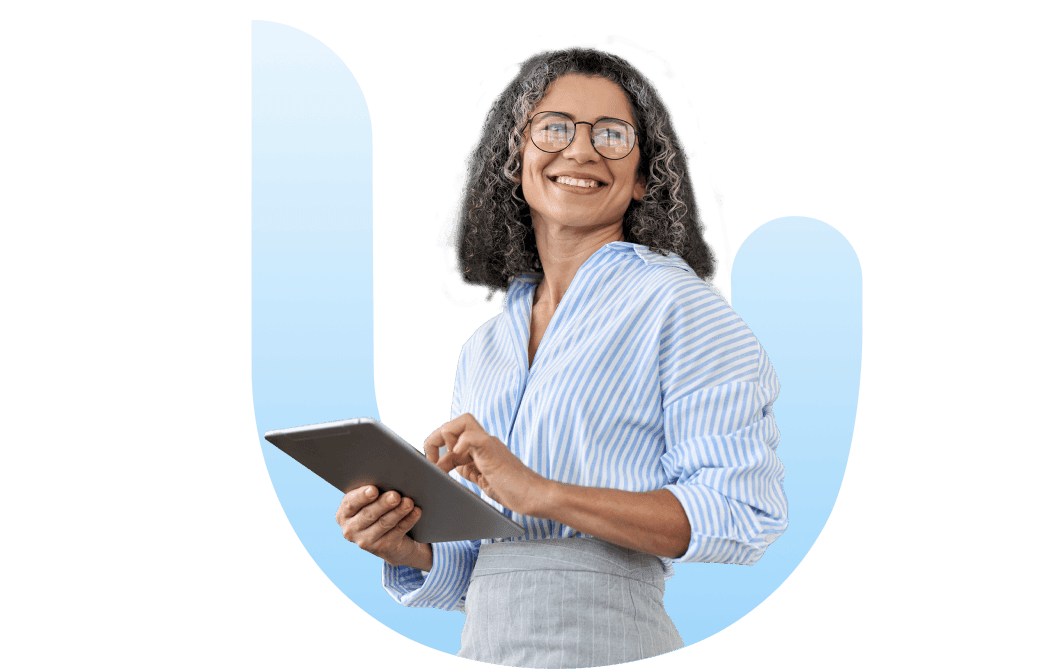
Discover the benefits of a transparent organization!
Try our free platform and strengthen the culture of openness in your team.
Workplace Environment
Yeva Bartkiv
Copywriter
Published
2025-07-24
Reading time
7 min
Table of contents
Subscribe to our newsletter
Workplace incidents are inevitable across industries - from near misses and minor injuries to major accidents and fatalities. But what truly separates high-performing safety cultures from reactive ones is how these incidents are handled.
Timely reporting, thorough investigation, and corrective actions can prevent future incidents and improve both legal compliance and workplace safety. This guide provides a step-by-step approach to effective incident reporting and incident investigation.
Whether you are an HR professional, EHS leader, line manager, or small business owner, understanding how to report and investigate a workplace incident properly is essential for protecting your workforce and complying with regulations such as OSHA or RIDDOR.
Let’s begin with the fundamentals: why is it important to report incidents in the workplace?
Without proper reporting, unsafe conditions remain hidden, and valuable opportunities to improve are lost. Underreporting or inadequate documentation increases legal risk, limits access to workers' compensation, and allows similar incidents to reoccur.
Clear and consistent workplace incident reporting helps organizations:
The first step in the incident investigation process begins with proper reporting. Everyone in the organization should know how to report a workplace incident, whether it's an injury, near miss, or property damage.
Documentation must be detailed and objective. A clear investigation report sets the foundation for practical analysis and corrective action. When completing a workplace incident report, be sure to gather the following:
Delays in launching an incident investigation can result in the loss of physical evidence, unreliable memories, and missed opportunities to intervene.
A prompt and organized investigation process should begin as soon as the incident is reported - ideally within 24 hours.
An effective investigation team may include:
The investigation team must approach the incident with objectivity, professionalism, and empathy. Avoid assigning blame prematurely; instead, focus on gathering information and understanding the true circumstances of what happened.
One of the most critical steps in any accident investigation is collecting relevant information from the scene of the incident. The goal is to recreate the sequence of events and uncover all contributing factors.
Use open-ended questions to encourage detailed responses. Avoid leading the witness or implying fault. For example:
Ensure all interviews are documented, signed, and securely stored.
Many workplace incident investigations stop short at human mistakes or procedural violations. While those are important, it's essential to identify the root causes of the incident, which often lie deeper.
Root cause analysis is a method used to identify the fundamental breakdowns that led to the incident. It seeks to answer not just what happened, but why it happened, and why the conditions that allowed it to happen were in place.
Common root causes include:
This step is vital for designing corrective actions that prevent recurrence rather than applying surface-level fixes.
After identifying the root causes, the next step is implementing strong and effective corrective actions. This stage ensures lessons are applied, risks are mitigated, and similar incidents are prevented.
Corrective actions address both immediate hazards and systemic weaknesses. For example:
Follow-up evaluations must be conducted to verify the effectiveness of corrective actions over time.
Finalize the incident investigation by compiling a comprehensive investigation report. This document should include:
Store reports in a centralized database as part of your management system, and ensure accessibility during audits or inspections.
Effective incident handling involves leveraging experience to prevent future incidents. This means sharing key findings across departments and reinforcing those lessons through:
Managing workplace incident reports and coordinating a thorough incident investigation process can be challenging, especially without the right tools and resources.
That’s where FaceUp comes in. FaceUp offers a modern, digital solution designed to simplify the process of improving safety culture in the workplace for HR professionals, safety officers, and business leaders.
By integrating FaceUp into your safety management system, you empower your teams to act swiftly, document thoroughly, and learn continuously, reducing the likelihood of future workplace accidents.
Regulatory bodies like OSHA in the U.S. or HSE in the U.K. require that certain incidents be reported within specific timeframes:
Failure to comply with these requirements can result in penalties, litigation, or increased insurance premiums. Accurate incident reporting and thorough documentation help protect your organization.
A mature safety culture doesn’t stop at compliance. It continuously improves. Every incident investigation should be viewed as a learning opportunity - part of a living, breathing safety program.
Steps to embed findings into your culture:
Encourage ongoing feedback from employees on work environment issues, PPE, and unsafe conditions. Proactive reporting is one of the strongest indicators of a resilient safety management culture.
Whether it’s a near miss, equipment failure, or serious injury, every workplace incident is a critical signal. By applying a structured, proactive, and transparent approach to incident reporting and investigation, you not only comply with legal requirements but also protect your people, enhance your processes, and drive long-term business value.
From gathering physical evidence to conducting a root cause analysis, and from interviewing interviewees to implementing corrective actions, this step-by-step guide equips you to lead safer, smarter, and more sustainable operations.
To take your incident management to the next level, explore how FaceUp can support your safety goals by streamlining reporting, investigation, and follow-up processes. Book a demo today to see how it works.
Try our free platform and strengthen the culture of openness in your team.
Keep Reading
Yeva Bartkiv2025-07-225 min
Whistleblowing
Yeva Bartkiv2025-07-156 min
Workplace Environment
Yeva Bartkiv2025-07-107 min
Legal & Compliance
Yeva Bartkiv2025-07-075 min
Legal & Compliance